Diecasting has become an essential part of Malaysia’s manufacturing industry, supporting key sectors such as automotive, electronics, and industrial machinery. The process, which involves injecting molten metal into a mold under high pressure, allows manufacturers to create durable and precise components in large volumes. With the country’s well-established industrial infrastructure and skilled workforce, Malaysia has positioned itself as a competitive hub for Diecasting production. The industry benefits from modern facilities, cutting-edge technologies, and strict quality control measures that meet global manufacturing standards. Many international companies have chosen Malaysia as a strategic location for their Diecasting operations due to its cost-effective production capabilities and access to major markets. As the demand for lightweight and high-strength metal components continues to rise, Malaysia’s Diecasting industry is expected to expand further, contributing significantly to the country’s economic growth.
The automotive industry is one of the largest consumers of die-cast components, and Malaysia plays a key role in supplying high-quality metal parts for vehicles. Diecasting is widely used in the production of engine blocks, transmission cases, and structural components that require both strength and lightweight properties. With the growing emphasis on fuel efficiency and electric vehicles, automotive manufacturers are increasingly turning to aluminum Diecasting to reduce the weight of their vehicles. Malaysian Diecasting companies are known for their ability to produce complex automotive parts with high precision, adhering to international quality certifications such as ISO 9001 and IATF 16949. Many local firms have also formed partnerships with global car manufacturers, allowing them to export their products to markets in Europe, the United States, and Asia. The continued advancements in automotive engineering and the shift toward sustainable mobility solutions will further drive demand for die-cast components in Malaysia.
Beyond the automotive sector, the electronics and telecommunications industries heavily rely on Diecasting for the production of precision metal parts. Malaysia has established itself as a leading hub for electronics manufacturing, with many multinational companies setting up production facilities in the country. Die-cast components are essential for various electronic devices, including smartphones, laptops, and home appliances, as well as for industrial equipment such as power supply units and network infrastructure. The ability to create intricate designs with tight tolerances makes Diecasting an ideal manufacturing method for these applications. To keep up with the fast-paced electronics industry, Malaysian Diecasting firms have adopted high-pressure Diecasting (HPDC) and computer-aided design (CAD) technologies to enhance precision and efficiency. As consumer demand for advanced electronic devices continues to grow, Malaysia’s Diecasting industry is poised to support the increasing need for reliable and high-quality components.
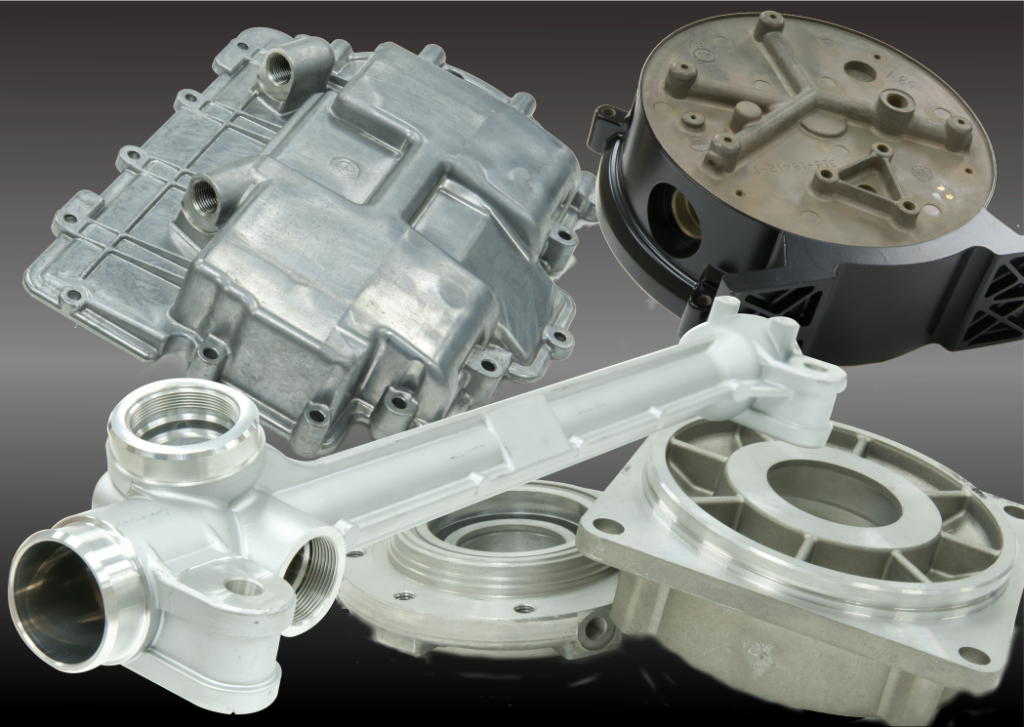
The consumer goods and industrial machinery sectors also benefit from Malaysia’s robust Diecasting industry, as manufacturers require durable and cost-effective metal parts for various applications. Household appliances, power tools, and mechanical equipment often incorporate die-cast aluminum or zinc components to improve their strength and longevity. Many die casting company Malaysia work closely with designers and engineers to develop customized solutions that meet specific industry requirements. The use of advanced molding techniques and automated production systems has helped manufacturers increase output while maintaining product quality. With Malaysia’s strong supply chain network and efficient logistics infrastructure, local Diecasting firms can efficiently deliver components to domestic and international markets. As industries continue to seek innovative ways to enhance product performance and reduce manufacturing costs, the demand for die-cast solutions is expected to remain strong.
Sustainability has become a growing focus in Malaysia’s Diecasting industry, with companies striving to implement environmentally friendly practices. Many manufacturers are investing in energy-efficient machinery, adopting recycling initiatives, and optimizing production processes to minimize material waste. The use of lightweight metals such as aluminum not only benefits industries looking to reduce their carbon footprint but also aligns with global efforts to promote sustainable manufacturing. Additionally, Malaysia’s government has introduced initiatives to encourage green technologies and Industry 4.0 advancements, further supporting the adoption of eco-friendly Diecasting processes. By integrating smart manufacturing technologies, including real-time monitoring and predictive maintenance, Diecasting firms can improve efficiency while reducing environmental impact. These sustainable practices ensure that Malaysia’s Diecasting industry remains competitive and aligned with international standards.
Looking ahead, the future of Diecasting in Malaysia appears promising as the industry continues to evolve with advancements in automation, robotics, and material innovations. The integration of artificial intelligence (AI) and digital twin technology is expected to enhance process optimization and quality control, leading to even greater precision in manufacturing. As global demand for high-performance metal components continues to rise, Malaysia is well-positioned to strengthen its role as a leading Diecasting hub in Asia. The combination of strong government support, skilled labor, and continuous technological improvements will drive further growth in the sector. With a commitment to innovation and sustainability, Malaysia’s Diecasting industry is set to remain a key contributor to the country’s manufacturing landscape, offering high-quality solutions to industries worldwide.
Leave a Reply